Grinding Machines
SUNNY
MACHINERY
Manual Saddle Type Surface Grinding Machine
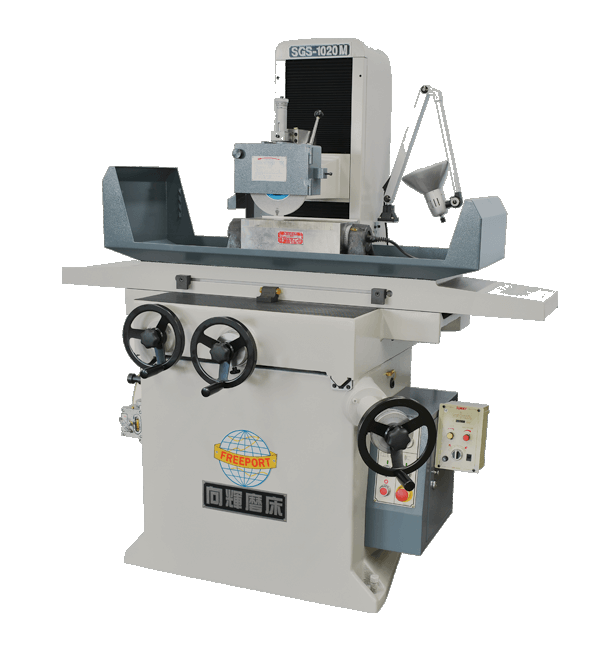
Features and Benefits
When it comes to precision grinding, the Manual Saddle Type Surface Grinding Machine is an excellent choice. Here are some of its top features and benefits:
Worktable Slide-way: One V One Flat
Our machine’s worktable slide-way is made of high-temperature, precision-ground special alloy steel. This ensures that your operation is not only simple and effective, but also highly precise thanks to precision steel balls.
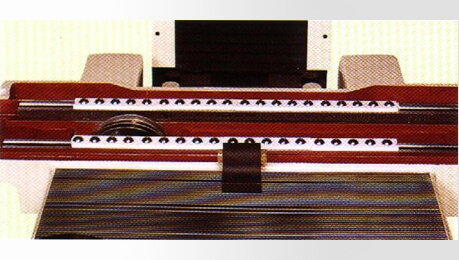
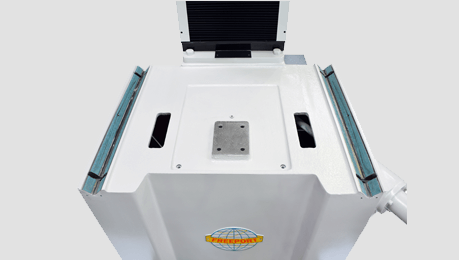
Cross-feed Slide-way: Twin V
Our machine’s cross-feed slide-way uses low friction Teflon to create steady and fluid saddle movements. This ensures that your grinding is efficient and smooth, with no interruptions or hiccups.
Optional Microns Adjust with Rapid Vertical Feed (MR Type)
Our machine’s optional microns adjust with rapid vertical feed (MR type) feature uses low friction Teflon to ensure that the minimum micron adjustment is 0.002mm. With the pushbutton quick vertical feed, you’ll be able to increase your grinding efficiency and enjoy stable, smooth saddle movements.
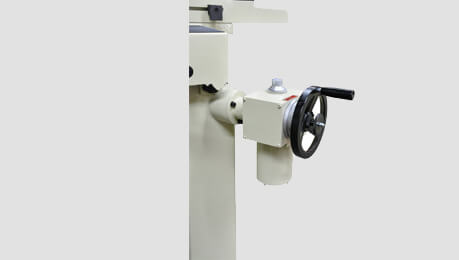
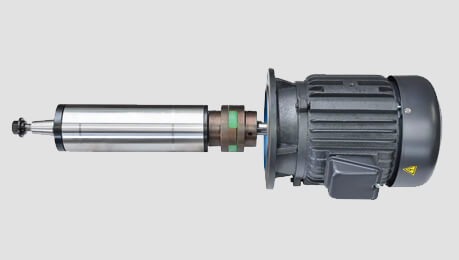
Spindle & Motor Set
Our machine’s spindle and motor set is built for high precision and minimal vibration. We use four super precision P4 grade angular ball bearings in a high precision, internally constructed cartridge type spindle. And to provide the most torque and minimize vibration, a V3 grade motor is integrated with the spindle set via couplings for direct transmission.
Saddle Type Surface Grinder
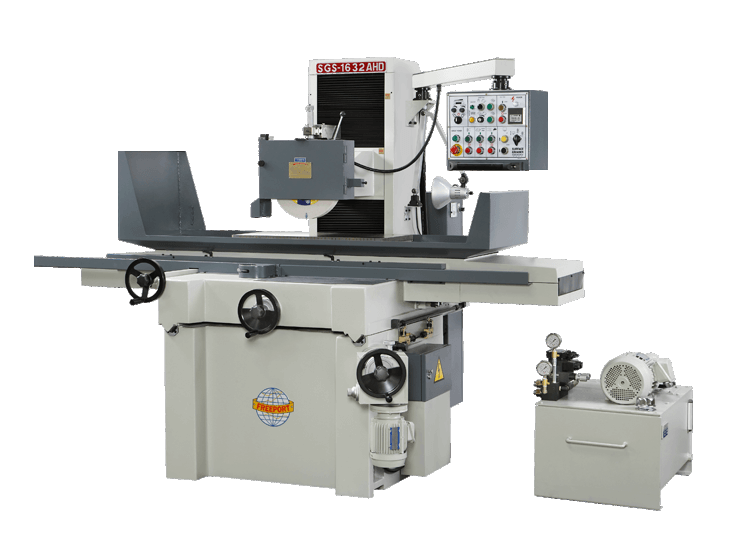
Features and Benefits
If you’re looking for a high-quality surface grinder that’s built to last, the Saddle Type Surface Grinder is an excellent choice. Here are some of its top features and benefits:
Worktable Slide-way: One V One Flat
Our machine’s worktable slide-way uses low friction Teflon to create steady and fluid saddle movements. This ensures that your grinding is efficient and precise, with no interruptions or hiccups.
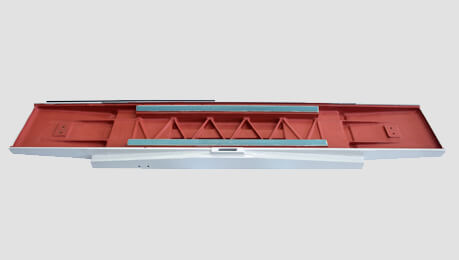
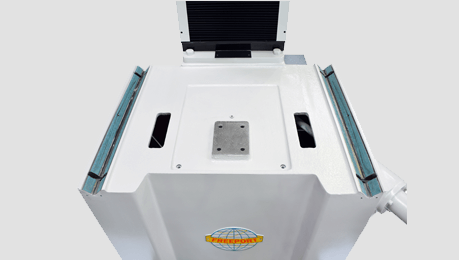
Cross-feed Slide-way: Twin V
Our machine’s cross-feed slide-way also uses low friction Teflon to provide smooth and stable saddle movements. You’ll be able to enjoy consistent grinding performance, no matter what your needs may be.
Spindle & Motor Set
Our machine’s spindle and motor set is built for precision and minimal vibration. We use four super precision P4 grade angular ball bearings in a high precision, internally constructed cartridge type spindle. And to provide the most torque and minimize vibration, a V3 grade motor is integrated with the spindle set via couplings for direct transmission.
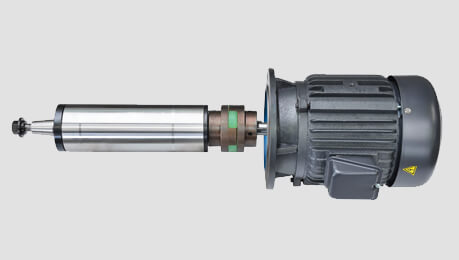
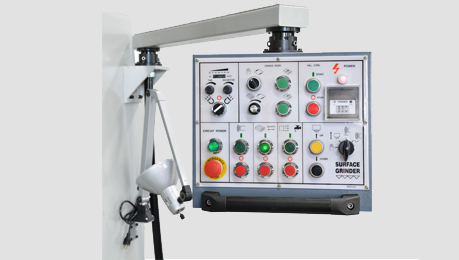
Control System (AHD Type)
Our machine’s control system (AHD type) is easy to use and highly robust. All gears and shafts have been heat-treated and hardened for maximum durability. And with 0.002 to 0.02 mm vertical feed micron adjustment (10 phase), you’ll be able to choose between 1 and 999 times for the vertical feed.
Control System (SD/PD Type)
Our machine’s control system (SD/PD type) uses an AC servo motor for vertical feeding and features a control panel LED display for precise numerical wheel setting. You’ll also be able to establish automatic cross feed travel limitations with the control panel and choose from several vertical feed modes.
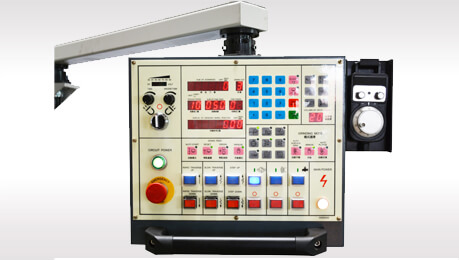
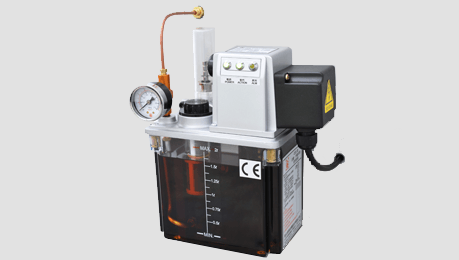
Lubrication System
Our machine’s lubrication system is completely automated, ensuring that your machine stays well lubricated and in top condition for years to come.
High Precision Column Type Surface Grinding Machine with Robust Upper Column
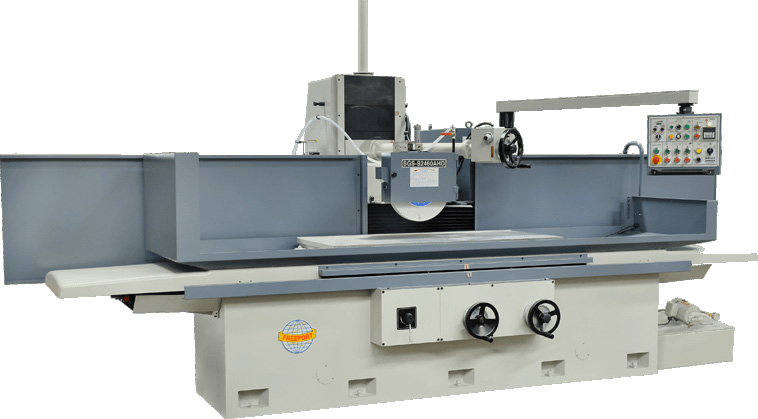
Features:
Robust Upper Column
The machine features twin walls that provide maximum stability during operation.
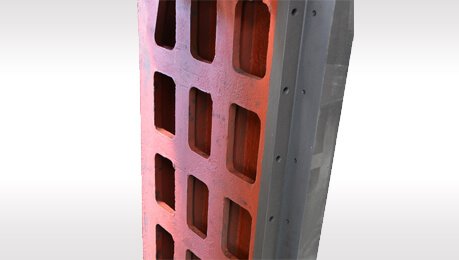
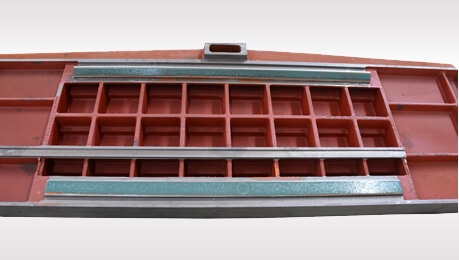
Worktable Slide-way
The worktable slide-way features one V and one flat surface to ensure steady and fluid saddle movements. Additionally, a PLC device enables quick and accurate cross-feed setup.
Cross-feed Column Slide-way
The cross-feed column slide-way features twin V surfaces to ensure smooth and stable saddle movements.
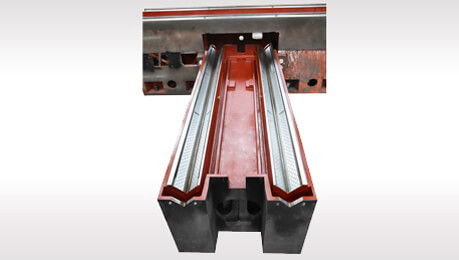
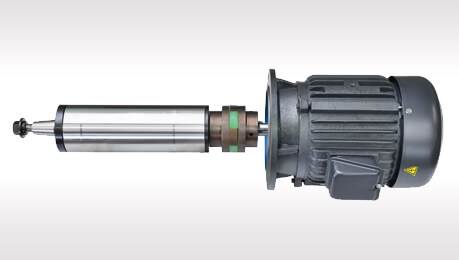
Spindle & Motor Set
The machine uses four super precision P4 grade angular ball bearings in a high precision, internally constructed cartridge type spindle. The spindle is integrated with a V3 grade motor via couplings for direct transmission, providing maximum torque and minimizing vibration.
Control System (AHD Type)
The hang-type control panel with dual rotation makes the machine easy to operate. It allows for micron adjustment for vertical feed between 0.002 and 0.02mm (10 phase) and a range for the number of vertical feed times from 1 to 999. With the control panel, cross-feed travel restrictions can be established and modified.
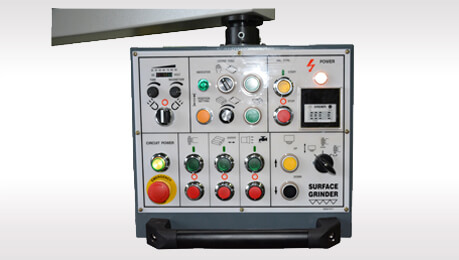
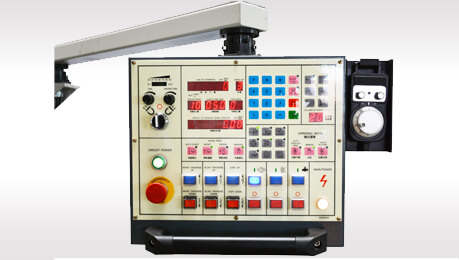
Control System (SD/PD Type)
This system uses an AC servo motor for vertical feeding and features a control panel LED display that allows for precise numerical wheel setting. The control panel also enables the establishment of automatic cross-feed travel limitations and offers several vertical feed modes, including Automatic Manual and a pulse generator for microns.
Lubrication System
The machine features a completely automated lubrication system to ensure smooth and uninterrupted operation.
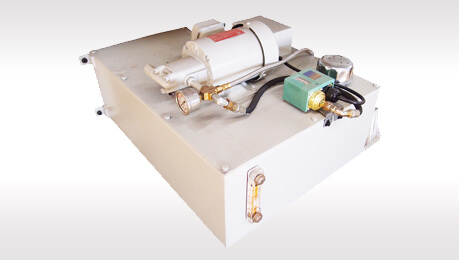
High-performance Heavy Duty Column Type Surface Grinding Machine
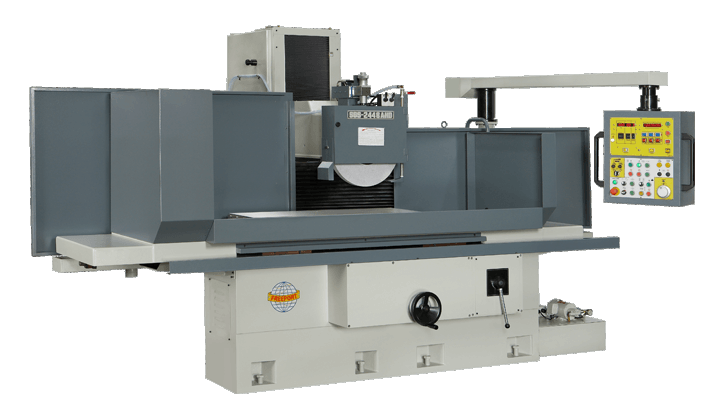
The heavy-duty column type surface grinding machine is designed to deliver high-performance results. It features a robust mechanism, a DC servo motor, and a solenoid valve hydraulic system that work together to ensure the highest level of efficiency for all types of grinding tasks.
Key features of the machine include:
Upper column
The improved net type double wall construction provides stability and grinding accuracy. Hydraulic weight balancing relieves ball-screw vertical feed loads, which increases the lifespan of the servo motor and vertical ball-screw. This ensures sensitivity and accuracy of vertical feed.
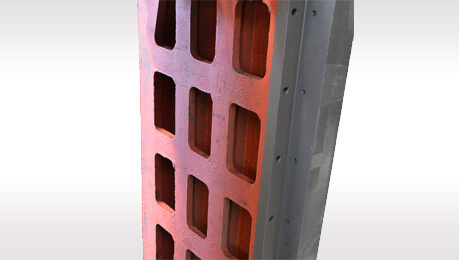
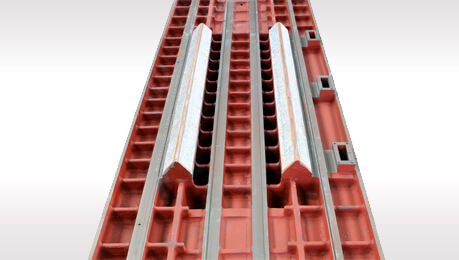
Worktable slide-way
The twin V slide-way uses low friction Teflon to create steady and fluid saddle movements. The modern hydraulic system with solenoid valve allows for step-less speed adjustment and steady, smooth worktable movements at a speed range of 1 ~ 26M/min.
Cross-feed column slide-way
The twin V slide-way uses low friction Teflon to create steady and fluid saddle movements. The control panel’s built-in PLC programme allows for quick setting of the grinding limits.
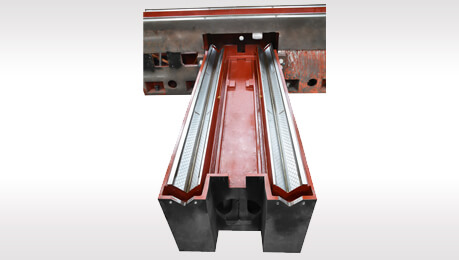
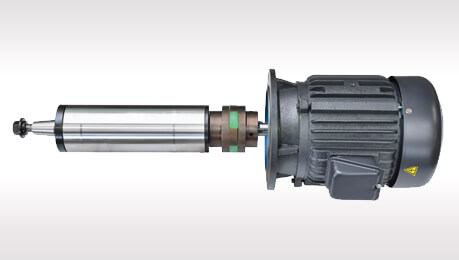
Spindle & Motor set
Six ultra-precision angular ball bearings of the CP4 grade are used in a cartridge type spindle set that is internally constructed and high precision. The spindle can grind with low noise, low heat rise, and high precision thanks to its superior structural design. A V3
grade motor is integrated with the spindle set via couplings for direct transmission to provide the most torque and minimize vibration.
Control System (AHD type)
A numerical control system that uses a vertically feeding DC servo motor. Superior sensitivity and accuracy of the wheel placement are ensured by encoders mounted on the servo motor and high precision ball-screw. The control panel allows for the establishment of automatic cross feed travel limitations. There are several vertical feed modes, including Automatic Manual and a pulse generator for microns.
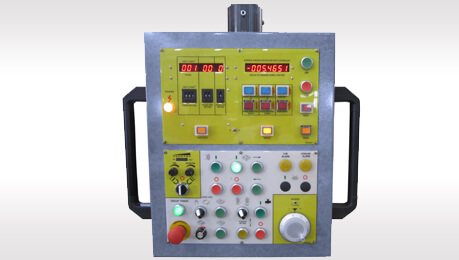
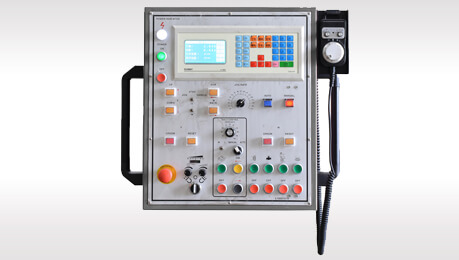
Control System (PNC type)
A numerical control system that uses DC servo motors for cross and vertical feed. An LCD display with digital inputs on the panel allows for easy operation on a variety of grinding applications. Control panel settings can be used to establish automatic cross
feed travel restrictions.
Lubrication System
The completely automated lubrication system ensures smooth operation and extends the lifespan of the machine.
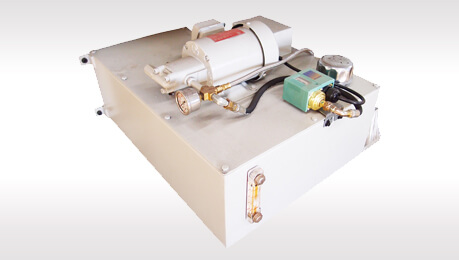
Single Head Double Column Surface Grinding Machine
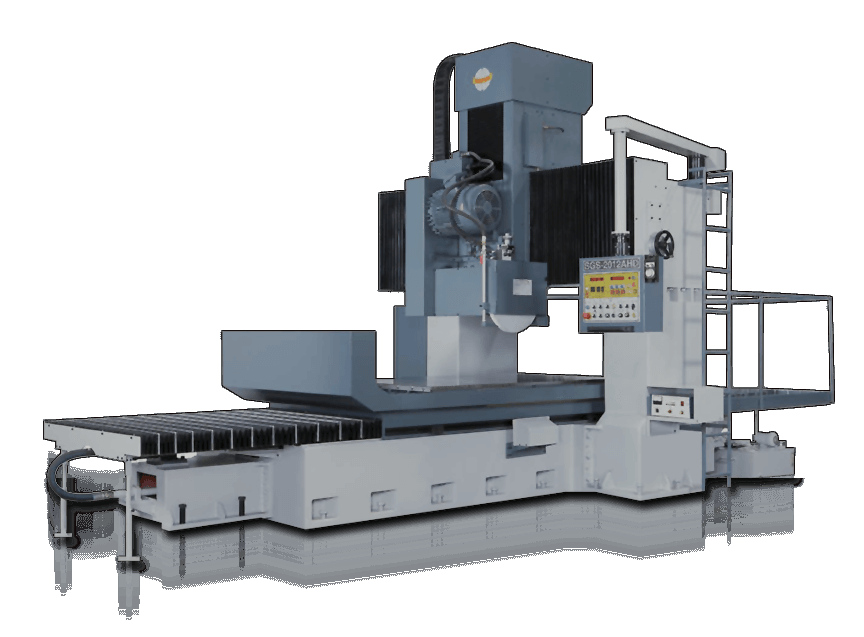
Features and Benefits
If you’re looking for a high-quality surface grinding machine, our Single Head Double Column Type model is an excellent choice. Here are some of its top features and benefits:
Structure
Our double column surface grinders are made of high-strength cast iron (FC30) that has undergone a tempering process to provide stiffness, stability, and longevity. Fixed cross-beam structures integrate the main machine, beam, and columns into a strong door shape, ensuring the stability of the machine.
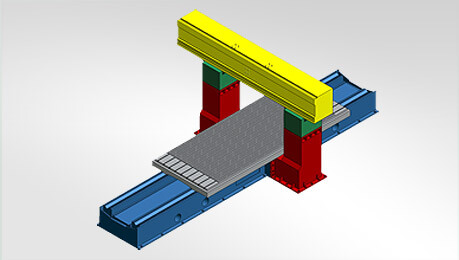
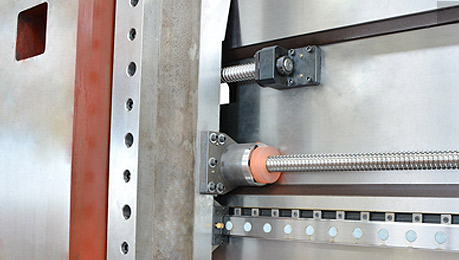
Movements
The machine base and work-table railroads feature a large twin V, allowing rock-steady table motions and maintaining the best alignment with balance. The grinding head moves smoothly and accurately over a THK ultra-precision grade linear guideway, delivering outstanding grinding results.
Spindle & Motor Set
Our cartridge type spindle set features six ultra-precision angular ball bearings of the CP4 grade, which ensure high precision and minimal noise and heat rise. The V3 grade motor integrated with the spindle set via couplings provides the most torque and minimizes vibration.
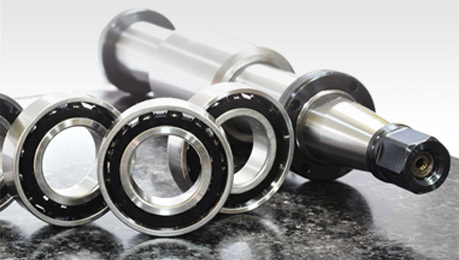
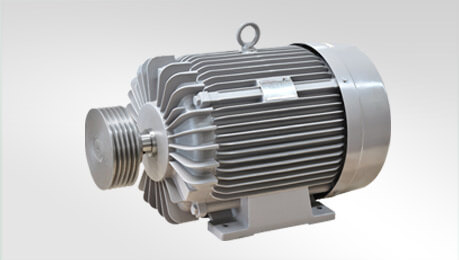
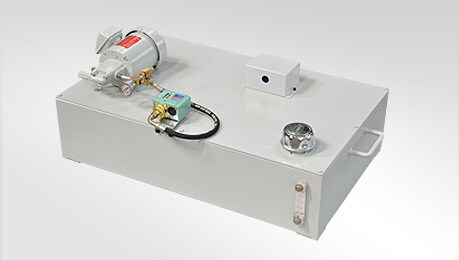
Lubrication
Lubrication prevents impacts from lubricant oil pulsation pressure and ensures smooth movements. The detecting sensor stops the table from moving to protect the railways when the lubrication oil pressure is not normal.
Hydraulic System
The proportional hydraulic valve is controlled using a precise electrical circuit. By directly adjusting the worktable speed through the control panel, the operator can increase work productivity. The Harbor Coolant System maintains Hydraulic Tank Temperature and ensures grinding accuracy while safeguarding hydraulic system components.
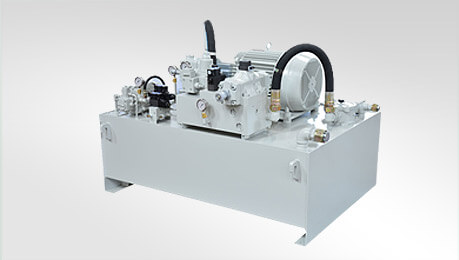
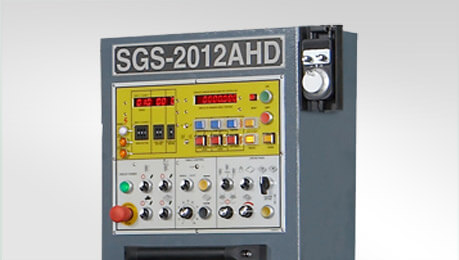
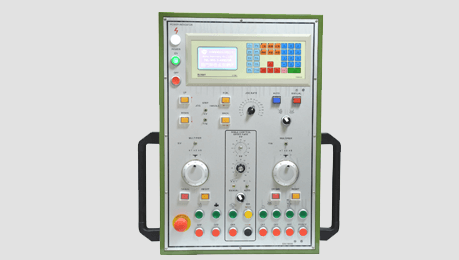
Control System
Our Single Head Double Column Type surface grinding machine comes in two control system types: AHD and PNC. The AHD type uses an AC servo motor for vertical feeding and allows for simple and accurate wheel positioning through the numerical display on the panel. The PNC type integrates all movements and functions into one panel, thanks to our own design of DSC based NC control system. The LCD screen displays on-panel digital inputs, making it simple to operate a variety of grinding applications.
Overall, our Single Head Double Column Type surface grinding machine is designed to deliver excellent precision and performance, while also being easy to operate and maintain. Whether you’re working in a production environment or a small workshop, this machine can help you achieve your grinding goals efficiently and reliably.
Twin Heads Double Column Surface & Slideway Grinding Machine
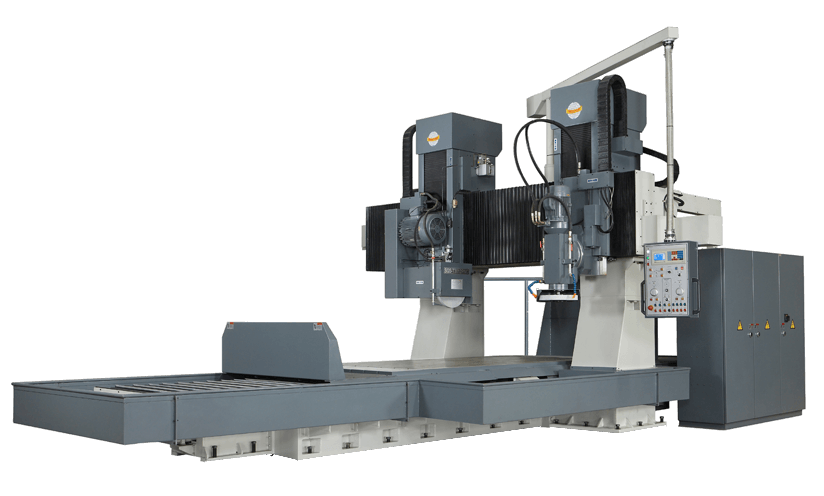
Features
Structure
Our twin heads double column grinding machines are made of high-strength casting iron (FC30) that has undergone a tempering process to provide stiffness, stability, and longevity. The fixed cross beam structure integrates the beam and columns into a robust door shape for optimal stability.
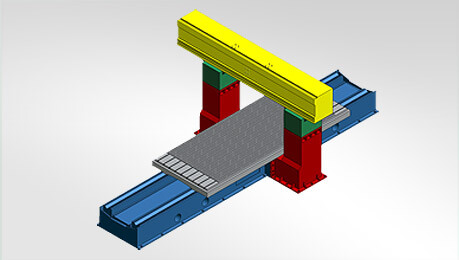
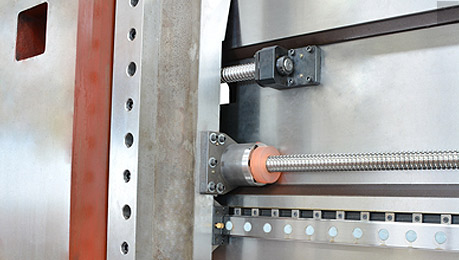
Movements
The large twin V on the machine base and work-table railroads allow for rock-steady table motions and maintain the best alignment with balance. Baldor AC servo motors power the grinding head’s vertical and longitudinal travel, which are guided by high-precision grade ball screws (PNC type). This feature enables precise positioning and feeding down to the micron level. The grinding head provides robust, smooth cross travel, as well as outstanding and accurate cutting ability. The vertical grinding head’s angular turn can be adjusted to be between +/- 90 degrees using a worm shaft transmission and an AC servo motor, allowing for quick and accurate angle forming grinding with an accuracy of 0.1 degrees.
Spindle & Motor Set
Our cartridge type spindle set uses six ultra-precision angular ball bearings of the CP4 grade, providing minimal noise, low heat rise, and excellent precision thanks to its superior structural design. All double column variants use high-torque V3 grade spindle motors from a Japanese manufacturer, providing minimal noise, little vibration, and great stability even after prolonged operation. The spindle set and V3 grade motor are integrated via couplings for direct transmission, providing the most torque and minimizing vibration.
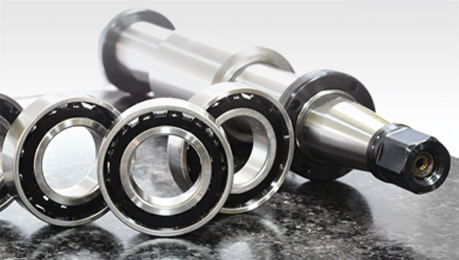

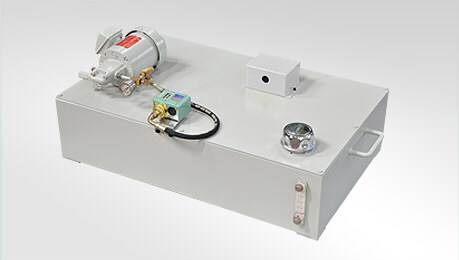
Lubrication
Smooth movements are ensured by lubrication, which prevents impacts from lubricant oil pulsation pressure. The detecting sensor stops the table from moving to protect the railways when the lubrication oil pressure is not normal.
Hydraulic System
The proportional hydraulic valve is controlled using a precise electrical circuit. The operator can directly adjust worktable speed through the control panel to increase work productivity. The Harbor Coolant System maintains hydraulic tank temperature and ensures grinding accuracy while safeguarding hydraulic system components.
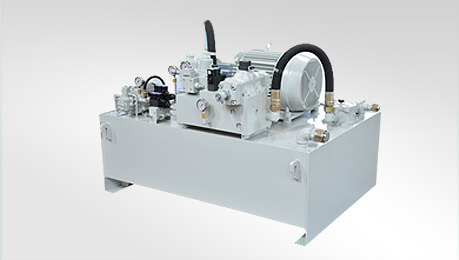
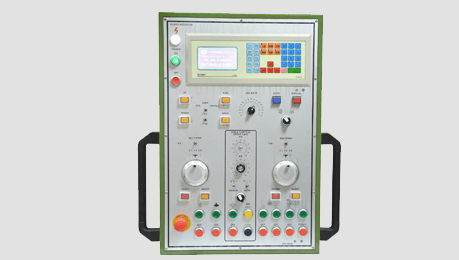
Control System (PNC type)
Our DSC-based NC control system integrates all movements and functions of the machine into one panel. The numerical control system uses cross and vertical feeds from AC servo motors. The on-panel digital inputs displayed on the LCD screen make it simple to operate a variety of grinding applications. The machine’s intuitive design and simple maneuvers eliminate the need for complicated programming, making it easy to operate.
Super Twin Heads Double Column Type Surface and Slideway Grinding Machine
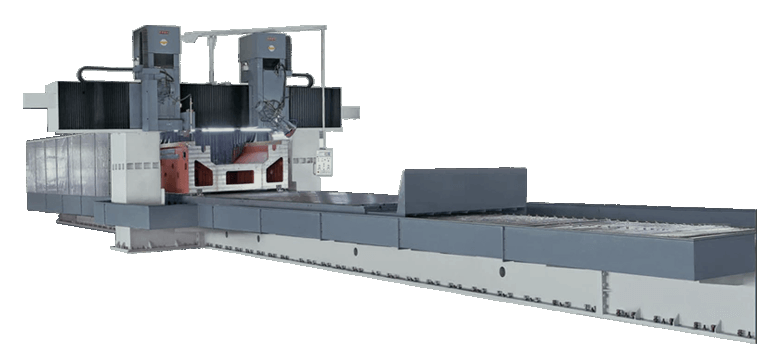
Features and Benefits
The Super Twin Heads Double Column Type Surface and Slideway Grinding Machine is a highquality machine designed for precision grinding. Here are some of the features and benefits of this machine:
Structure
- The machine is made of high-strength casting iron that has undergone a tempering process for stiffness, stability, and longevity.
- The fixed cross beam structures integrate the beam and columns into a single robust door shape, ensuring the stability of the machine.
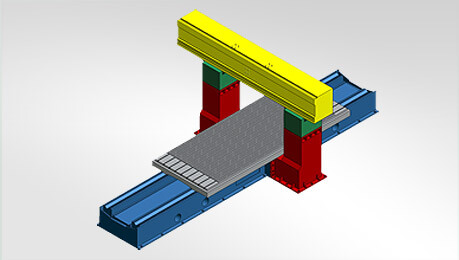
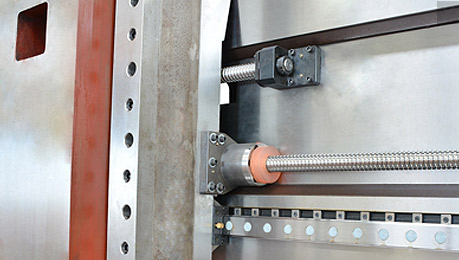
Movements
- The large twin V on the machine base and work-table railroads allows rock-steady table motions and maintaining the best alignment with balance.
- The Baldor AC servo motors power the grinding head’s vertical and longitudinal travel, which are guided by high precision grade ball screws.
- The grinding head is made of high-density strength steel and moves on ultra-precision grade linear roller bearings, offering remarkable cutting capabilities and a solid, smooth cross-travel.
- The vertical grinding head’s angular turn is powered by an AC servo motor via a worm shaft transmission, providing quick and accurate angle forming grinding.
Spindle & Motor Set
- Six ultra-precision angular ball bearings of the CP4 grade are used in a cartridge type spindle set that is internally constructed and high precision.
- All double column variants use high torque V3 grade spindle motors from the Japanese manufacturer, which have undergone rigorous testing with kinetic balance inspections.
- A V3 grade motor is integrated with the spindle set via couplings for direct transmission, providing the most torque and minimizing vibration.
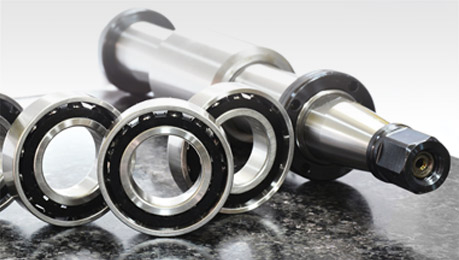
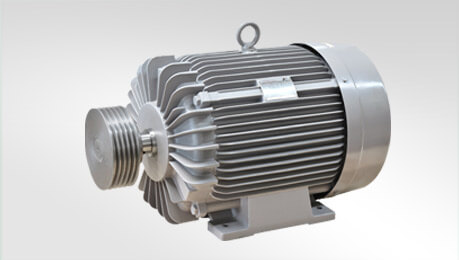
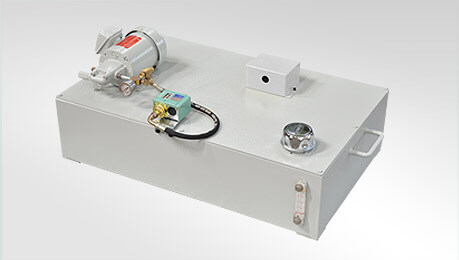
Lubrication
- Smooth movements are made possible by lubrication, which prevents impacts from lubricant oil pulsation pressure.
- The detecting sensor will stop the table from moving to protect the railways when the lubrication oil pressure is not normal.
Hydraulic System
- The proportional hydraulic valve is controlled using a precise electrical circuit, allowing the operator to directly adjust worktable speed through the control panel for increased productivity.
- The Habor Coolant System maintains Hydraulic Tank Temperature during many hours of operation to ensure grinding accuracy and safeguard hydraulic system components.
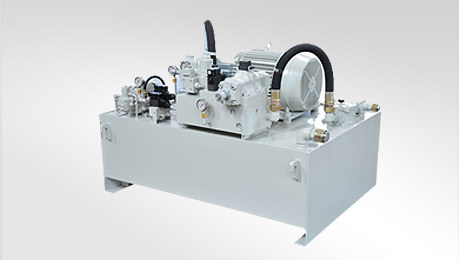
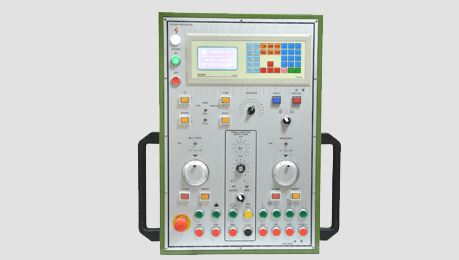
Control System (PNC type)
- The machine’s movements and functions are integrated into one panel by a DSC-based NC control system designed by the manufacturer.
- The on-panel digital inputs displayed on the LCD screen make it simple to operate a variety of grinding applications, eliminating the need for complicated programming.
In summary, the Super Twin Heads Double Column Type Surface and Slideway Grinding Machine is a robust, precise, and easy-to-operate machine suitable for various grinding applications. Its high-quality construction, precision movement, and intelligent control system make it a valuable addition to any machining facility.
PALMARY
Discover the Precision and Efficiency of PALMARY's Centerless Grinder
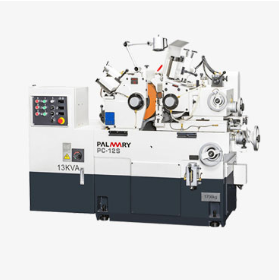
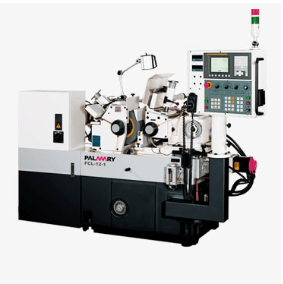
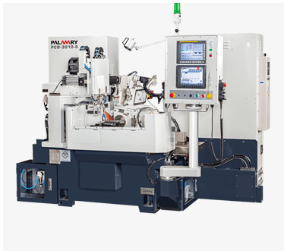
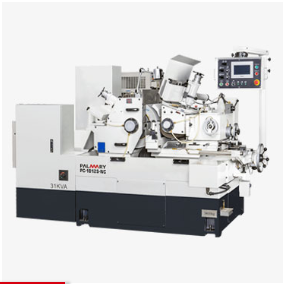
If you’re seeking high levels of accuracy and efficiency in your grinding operations, PALMARY’s Centerless Grinders are the ideal solution. Our servo-controlled model is expertly designed to meet the most demanding requirements and deliver the performance you need.
To ensure maximum rigidity and durability, we use only the finest materials in constructing our machines. Our machine frames are made from high-quality Melanite cast iron that undergoes heat treatment and stress relief prior to machining.
Here are some of the top features of our Centerless Grinders:
Precision Spindles
Our GW and RW spindles are crafted from alloy steel and undergo a meticulous production process that includes normalization, age and heat treatment, sub-zero treatment, and finishing machining and grinding.
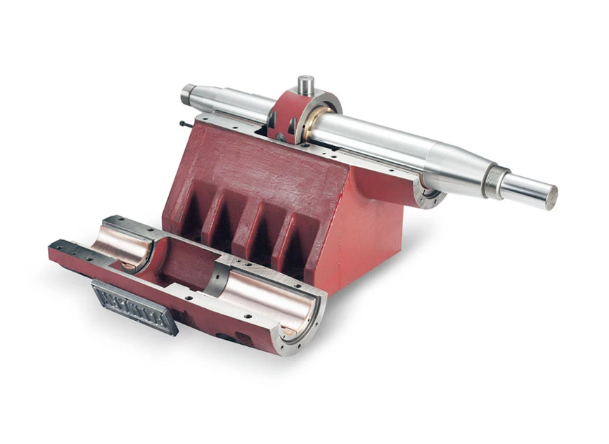
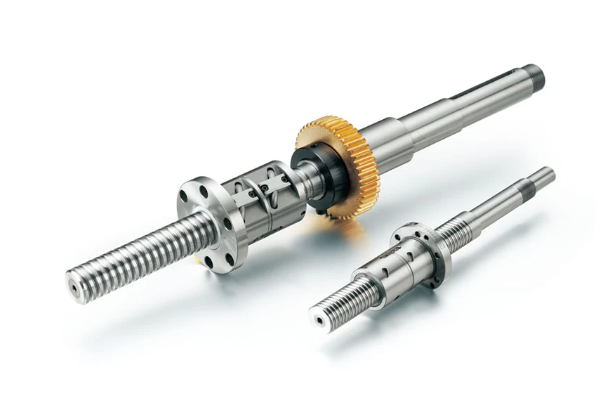
Feed Screw
Our feed screw is made from alloy steel that has been normalized, high frequency hardened, and precision ground to ensure high feeding accuracy and exceptional wear resistance.
Pressure Switch
Our pressure switch ensures safe starting of the GW and RW spindles by restricting their activation until oil enters the bearings, protecting the spindle bearings from damage.
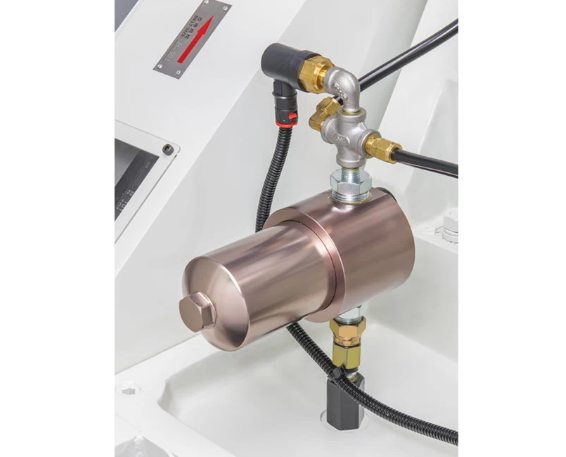
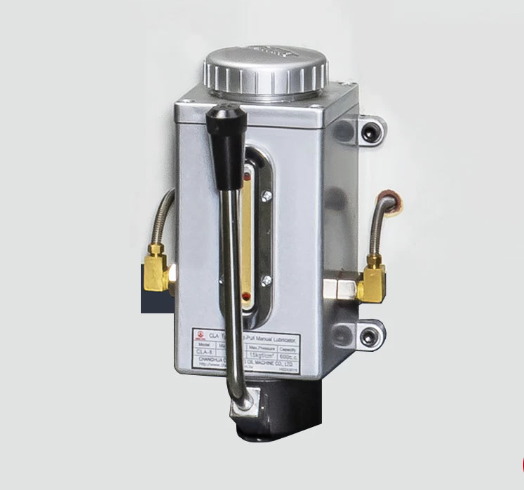
Lubrication System
Our automated lubricator ensures proper lubrication of the GW spindle, while our centralized lubrication system lubricates all slideways to ensure accurate feeding and optimal performance. Choose PALMARY’s Centerless Grinders for precision, efficiency, and reliability in your grinding operations.
Achieve Unmatched Grinding Accuracy and Flexibility with PALMARY's Cylindrical Grinder
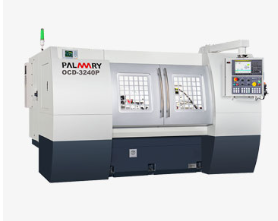
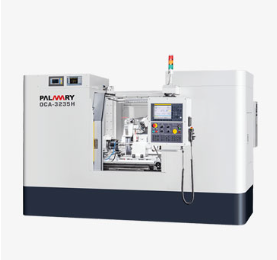
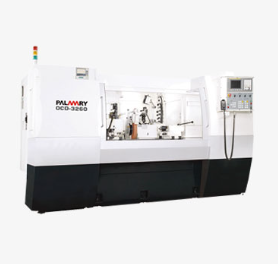
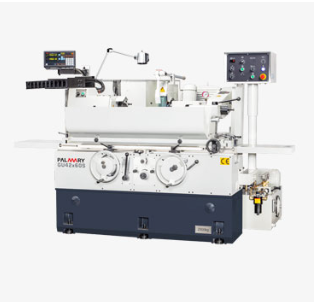
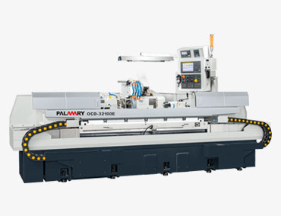
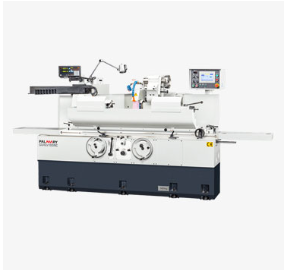
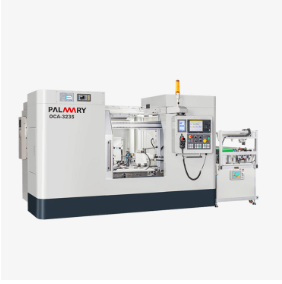
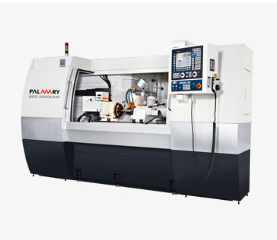
PALMARY’s Cylindrical Grinders are the epitome of structural stability, grinding accuracy, and ease of use. Our high precision machines offer unparalleled operating flexibility, allowing for a variety of grinding processes to be performed with ease. With our cylindrical grinder on your production line, you can expect to add value to your operations.
Here are some of the top features of our Cylindrical Grinders:
Stable and Rigid Spindle Head
Our precision bearings ensure maximum spindle stability, resulting in exceptional grinding accuracy for exterior diameter, internal diameter (if desired), and end face.
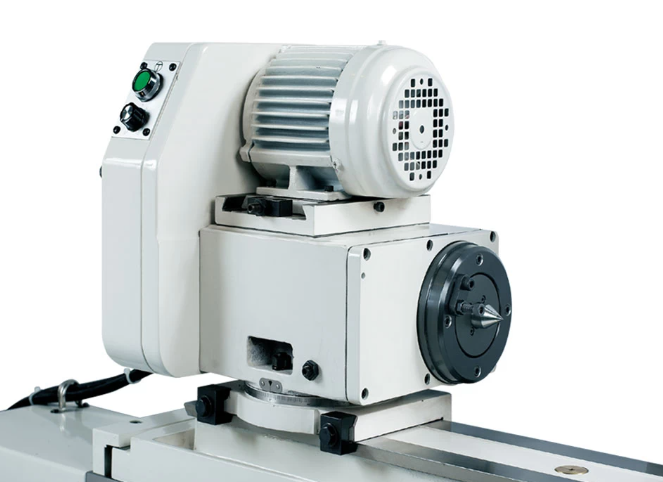
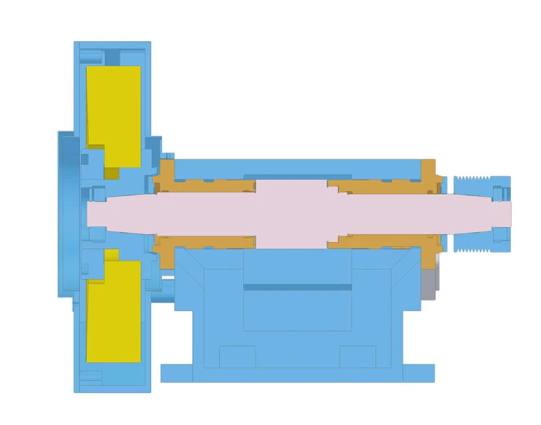
Special Hydrostatic Bearing
The unique hydrostatic bearing of our wheel spindle is ideal for precise grinding work. It operates at high speeds with no metal-to-metal friction, no heat generation, no deformation, and extremely high precision, making it perfect for continuous use.
Precision Wheel Head
Our carefully manufactured alloy steel grinding wheel spindle has been treated to a variety of processes, including precision grinding, mirror-effect treatment, normalization, tempering, carburizing, and sub-zero treatment, resulting in a highly precise and
durable machine.
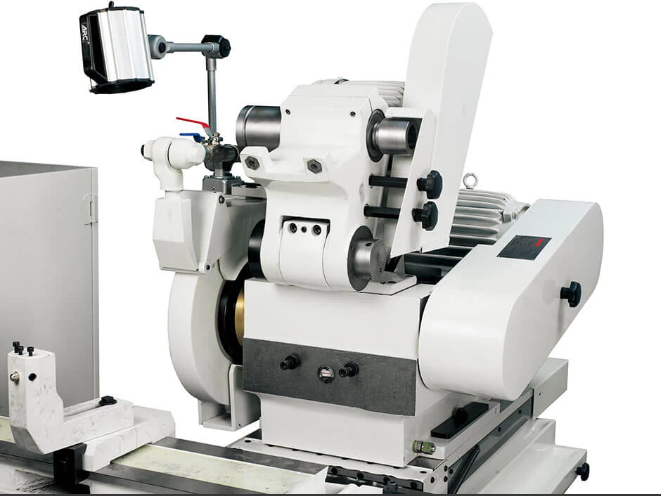
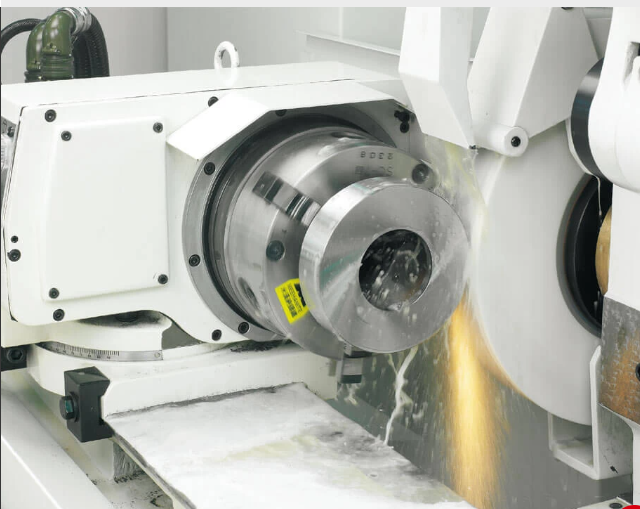
Various Grinding Applications
Our grinder is designed to perform a variety of grinding processes, including straight plunge grinding, shoulder grinding, traverse grinding, end face grinding, taper grinding, and even internal grinding (optional).
Choose PALMARY’s Cylindrical Grinder for unmatched grinding accuracy, flexibility, and ease of use.
Increase Your Grinding Accuracy and Productivity with PALMARY's Internal Grinder
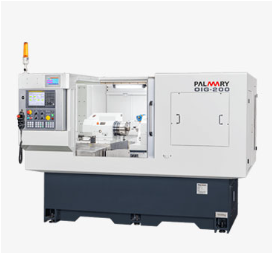
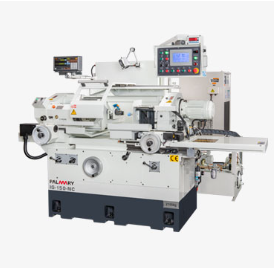
PALMARY’s NC series internal grinding machines are engineered with technical innovations and cutting-edge manufacturing processes to provide the best internal grinding equipment in the industry. Our NC series is equipped with a conversational operating interfacing control that improves and facilitates internal grinding.
Here are some of the top features of our Internal Grinders:
Convenient Grinding Operation
Our automated grinding operations include rough grinding, dressing, finish grinding, and spark out. This provides high accuracy, simple operation, and significantly increased productivity. Our grinder is perfect for flexible, small-quantity workplace grinding as well as mass manufacturing.
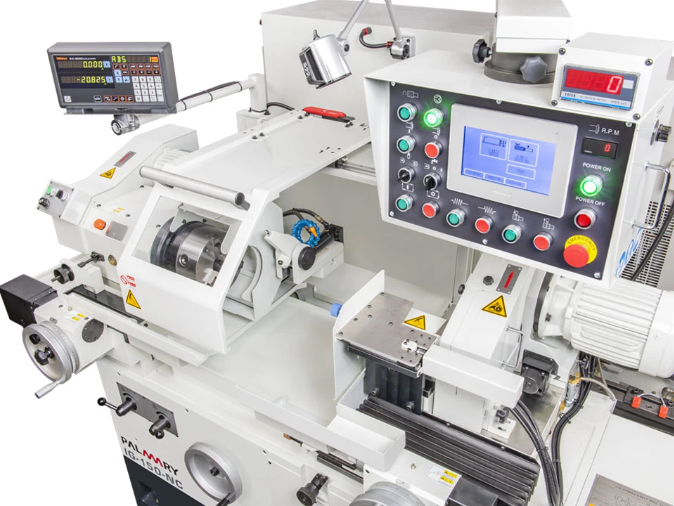
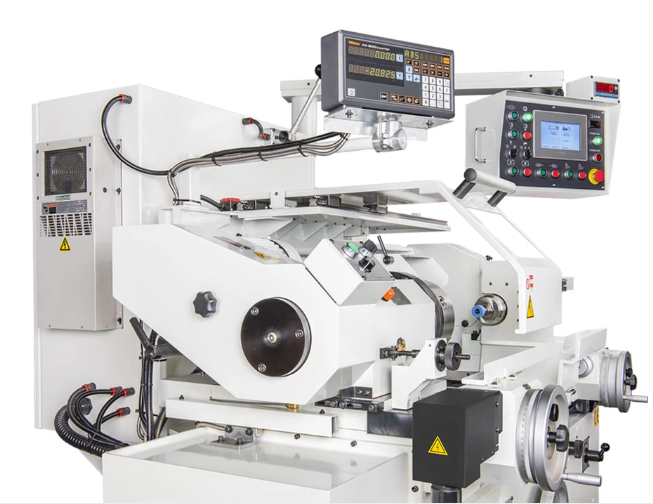
Precision Workhead Spindle
The workhead spindle is powered by a high precision roller bearing with excellent accuracy, high rigidity, and silent operation. Tapered workpieces can be ground by rotating the workhead clockwise 7° or anticlockwise 8°.
Slide Table
The reciprocating slide movement is powered by a hydraulic system that offers variable speed change and greater stability.
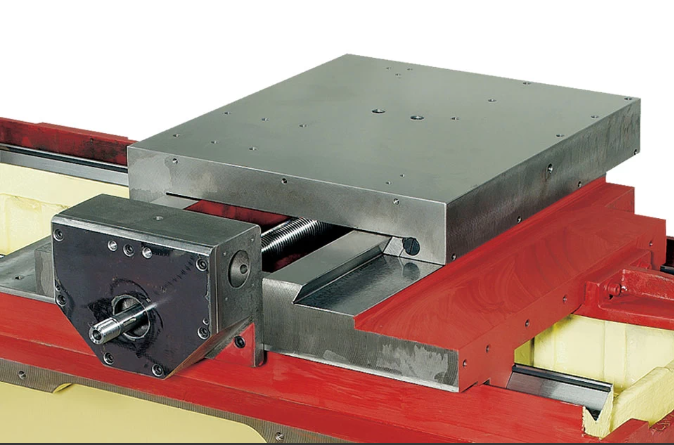
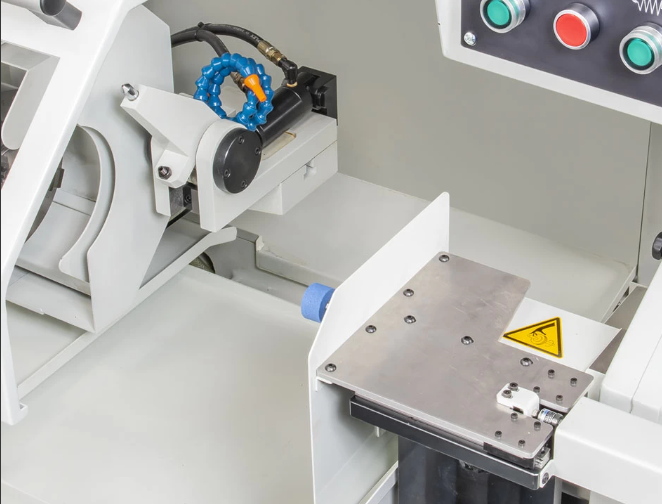
NC Controlled Auto Dressing with Compensation
Our internal grinder features an option to not compensate for dressing when using a diamond or CBN grinding wheel. A multiple dressing compensation mode can be selected to achieve the desired grinding quality for challenging sections.
Choose PALMARY’s Internal Grinder for convenient grinding operations, precision workhead spindle, stable slide table, and NC controlled auto dressing with compensation. Achieve increased grinding accuracy and productivity in your operations.
Precision Vertical Grinder for High-Performance Grinding
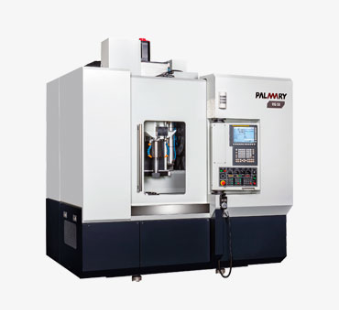
Our precision vertical grinders, designed and built by Palmary, offer exceptional stability, accuracy, and flexibility to meet the high demands of modern manufacturing. Each machine is crafted with human engineering design and peak performance concepts to ensure unrivaled grinding results.
The machine bed is made of premium Meehanite cast iron that has been heat-treated and stress-relieved for exceptional stability and no deformation, ensuring consistent, high-quality grinding.
Key features of our vertical grinders include:
High grinding accuracy
Our machines feature no self-weights of the workpieces or chucks that could generate vibration and run-out that could compromise the accuracy of grinding.
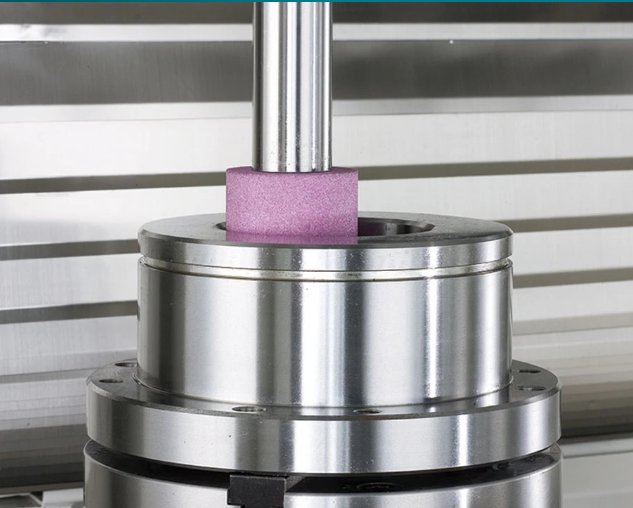
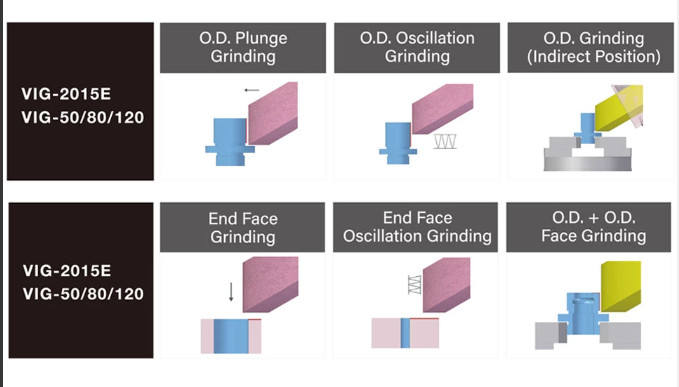
Various grinding techniques
Our grinders can handle a range of grinding techniques, including grinding the non-symmetrical portion between the internal hole and the external shape.
Easy chucking
Workpieces with odd shapes are simple to chuck, allowing for greater flexibility in grinding operations.
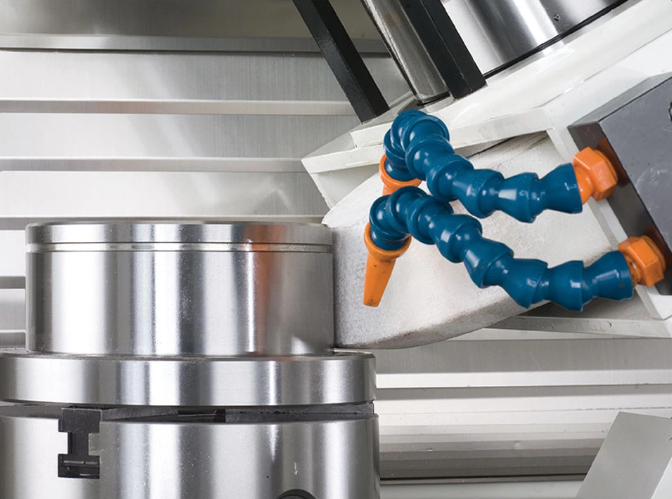
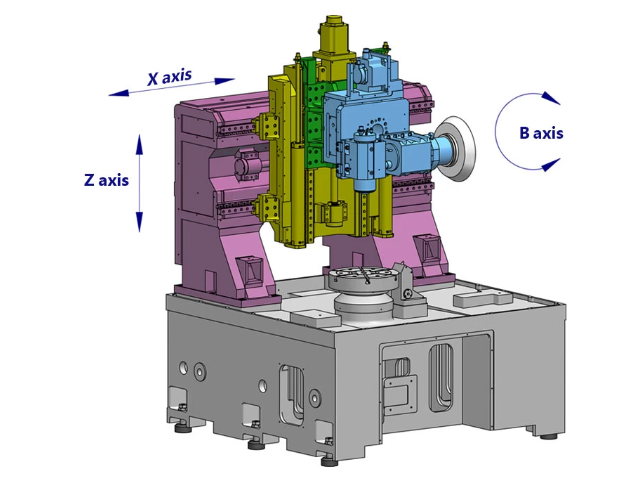
Heavy loading capability
Special cross-roller type linear guideways are installed on the X and Z axes, allowing for exceptionally heavy loading and providing greater stability during the grinding process.
Invest in our precision vertical grinders for superior grinding accuracy, versatility, and reliability in your manufacturing operations.
Special Purpose Grinder for Bearing Inner Diameter and Inner Groove Grinding
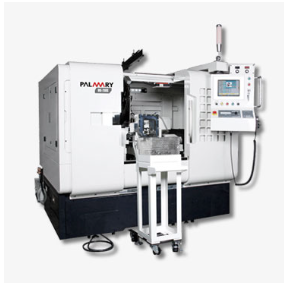
If you’re looking for an ideal grinding solution for thin workpieces, our special purpose grinder for bearing inner diameter and inner groove grinding is perfect for you. Built with the highest level of machine quality, our grinder is comparable to Japanese-made products, but at a more affordable price.
To help reduce machine body size and floor space, we’ve designed this special model with a built-in type of spindle. This provides clients with more industrial space and a more compact machine.
Here are some of the key features of our special purpose grinder:
Reduces cycle time
The bearing industry uses a work-head and a loading and unloading mechanism in tandem to operate while grinding the ID and inner groove, which reduces cycle time. An automatic loading system like a vibration feeder is also available as an alternative automation solution.
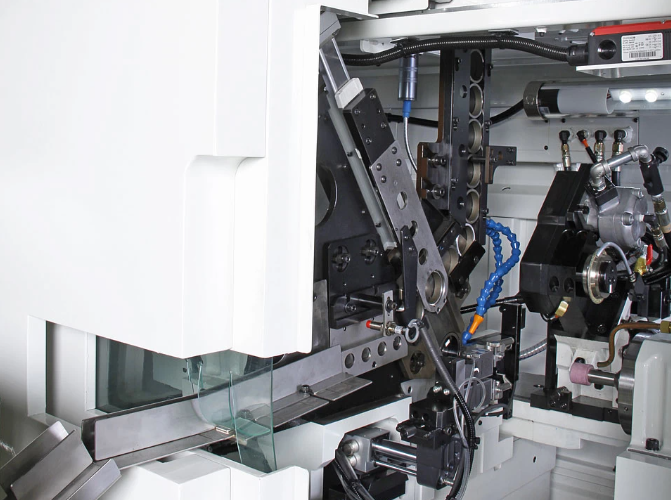
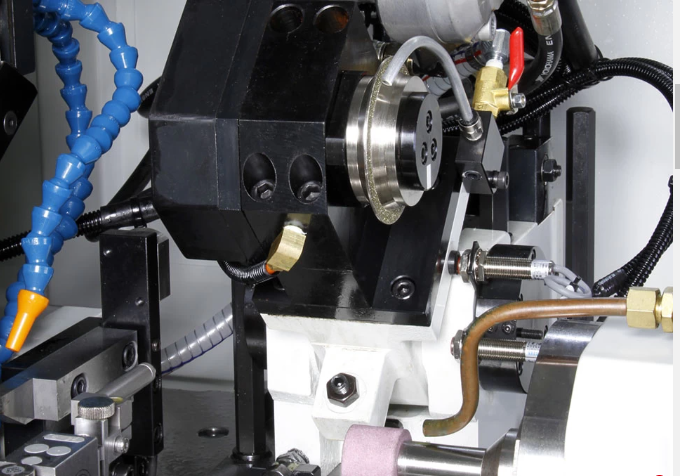
High-speed grinding efficiency
The high-frequency grinding wheel spindle provides fast, steady operation. The work-head’s permanent side base makes it simple to change the loading mechanism. To save cycle time during high-speed grinding, the X and Z axes utilize linear servo motors. The machine also includes an optional CBN wheel for improved grinding accuracy.
High accuracy
The machine has a digital readout on both axes, which enables extremely high accuracy, particularly for small and thin inner hole sections that are typically challenging to grind. An electronic work-head with a wide rotation and a centerless supporter is also included to make it easy to chuck thin workpieces without deforming.
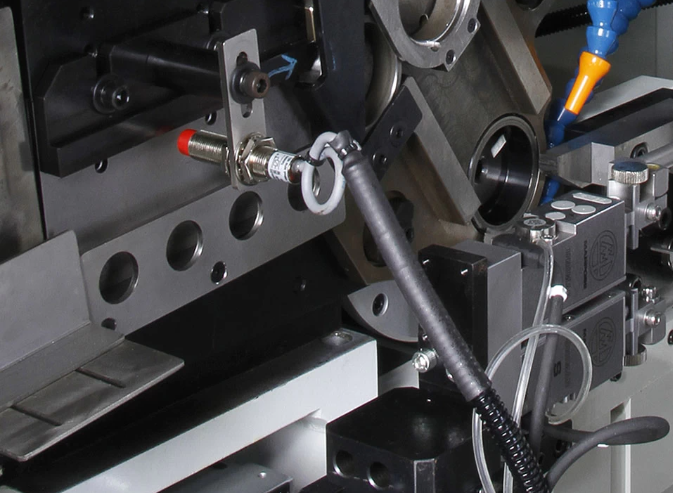
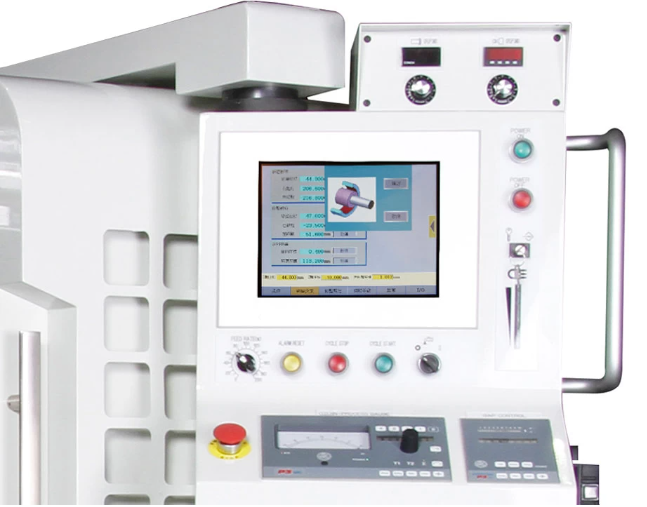
User-friendly
We’ve designed a PLC control panel that is simple to use for several types of CNC controllers. Clients can also select an optional digital readout or in-process ID gauge for high accuracy grinding needs.
High-Quality Surface Grinders for Precision and Productivity
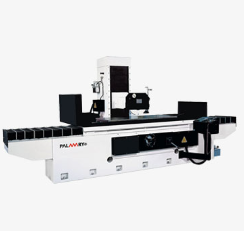
Our surface grinders are designed with precision and productivity in mind. We use strong cast iron and superior structural design to eliminate internal stress and ensure rigidity, stability, and accuracy.
Features of our surface grinders include:
- “H” series cross and vertical sideways coated with Turite-B for stable movement and durable accuracy
- P4 precision angular contact bearings for the spindle, ensuring accuracy within 2 and a cartridge design that is completely sealed and lubricated for high durability and accuracy
- Automatic down-feed AD5 (NG) for greater convenience in grinding operations (optional for “AH” series)
- Double-wall construction for main casting parts like the column and table to ensure rigidity and stability during heavy grinding
- Wide range of models to choose from, including manual, hydraulic, and servomotor operated
Our surface grinders are designed and manufactured to meet the needs of high accuracy and fine surface finish. Trust us to provide you with a surface grinder that meets your exact needs for precision and productivity.